

I'm interested to see what the engine will do with four independent valves providing total flexibility over valve events, allowing experimentation with lead, lag, expansion and timing etc without having to rebuild mechanical valve gear. For example, I'm crawling towards building a small horizontal steam engine with Arduino controlled electric valve gear. I want the printer to produce small plastic components for other projects. Arrives as a part built-kit, fairly basic, but allegedly produces reasonable results. I chose the model based on good reports - it's the go to choice at the moment for a low cost starter. Blender.Bought myself a Creality Ender 3-Pro printer for xmas and thought I'd report progress. Last but not least: for working with meshes, try using mesh modeler, e.g. * perform cuts or other BOPs in MeshDesign workbench (BOPs on meshes in FreeCAD are powered by OpenSCAD, which is not bundled with FreeCAD and needs to be installed separately). * make cylinders and whatever else for cuts/additions in Part/PartDesign/Draft Consider working with meshes, something like this: This usually results in a failed BOP.īut apart from that, it may actually be good enough for 3d-printing, because slicers can often repair the intersecting meshes by fusing them before slicing (or during slicing, I don't know).Īnother point: converting stl to solids can work, but it results in a whopping B-Rep model that is terribly inefficient and prone to faults. Joining things that intersect into a compound is generally a bad idea, because boolean operations (BOPs) assume that if they get a compound, there are no intersections within the compound. Before you do that it is important that your meshes is in as good a condition as possible.įreeCAD has a Mesh workbench witch can do some checking and fixing of the meshes.įollowing this advise I am quite certain that you will have better results.ĭarthjman wrote:"Fusion Failed" every time, I then found the compound that seemed to work.Compound always works but it doesn't actually do anything, apart from grouping the shapes you supplied into one shape.
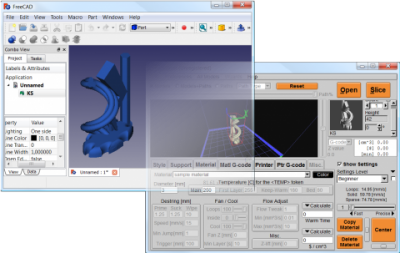
When importing meshes into FreeCAD you should not only Part:Create shape from mesh(witch creates a shell), but also run Part:Convert to solid. So if you select the last feature of your project and export this you should be ok.ġ If you run Part:Check geometry on Lids0001 you will find that it is a compond of 2 shells, it also has a lot of invalid faces and vertexes.Ģ If you run Part:Check geometry on HepaRim001 you will find that it is a shell.
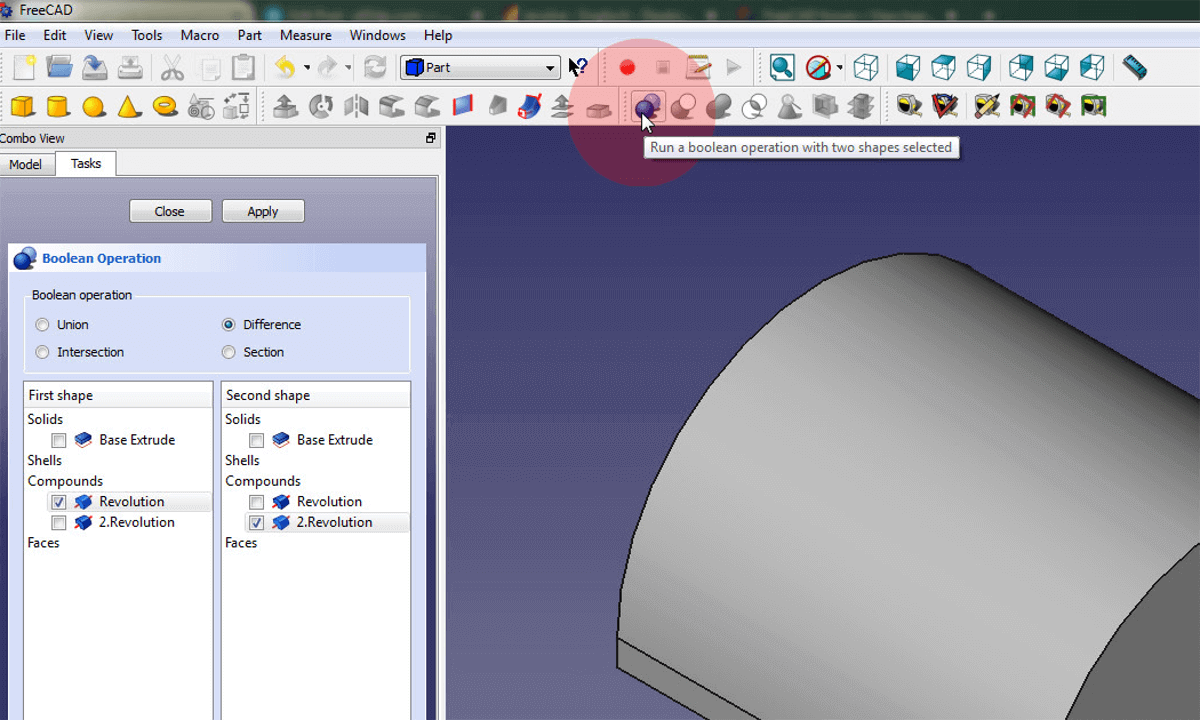
The items in the project tree is called features and should be considered snapshots of the design process, not actual parts that make out the last feature in the tree. When exporting to stl you are probably selecting all items of the project. Thank you for a wonderful post, with lots of information to base our help on Please, if anyone can help me figure out where I am going wrong, it would be much appreciated! I punched the holes this time with the Create-Cylinder/polar array/Boolean Cut Method, again according to documentation. I assume maybe the part is just too complex, I'm also assuming it has to do with my inadequacies at the program and not an issue with the program itself.įile 1 started an stl mesh, I converted to solid in FreeCAD, punched the holes in the bottom with polar pattern pockets, and that's really about itįile 2 started as 3 different stl meshes, they were converted to solids, then I tried to Boolean Union (according to tuts and documentation) but the "Fusion Failed" every time, I then found the compound that seemed to work. I have done some searching and haven't really found the same situation covered. Although I do no understand the difference between the meshing tessellation options, I tried all 3, first with default settings and then again after tweaking settings. I then figured I may have better luck turning the solids to mesh in FreeCAD before converting to STL, this results in the program freezing every time (I let it go for over three hours once, just to see if time was the factor). The first method attempted was to simply export as stl files, this resulted in stl files but the "holes" I had created either disappeared (file1) or turned into the physical cylinders that were used to boolean cut the holes (file2). I have found myself unable to convert from FreeCAD to an stl file for 3D printing. My files were so big I had to FTP them to here (File1) and here (File2) First off a BIG THANK YOU to everyone involved in the creation and ongoing support of FreeCAD, I am truly impressed at the depth of this program!
